Engineering Guidelines
Engineers and product designers need to consider all essential parameters to design an effective and functional dynamic seal. We are here to assist you with this process.
Several factors influence the performance of a shaft seal, including:
- Media
- Rotational speed
- Temperature
- Positioning
- Cleaning agents
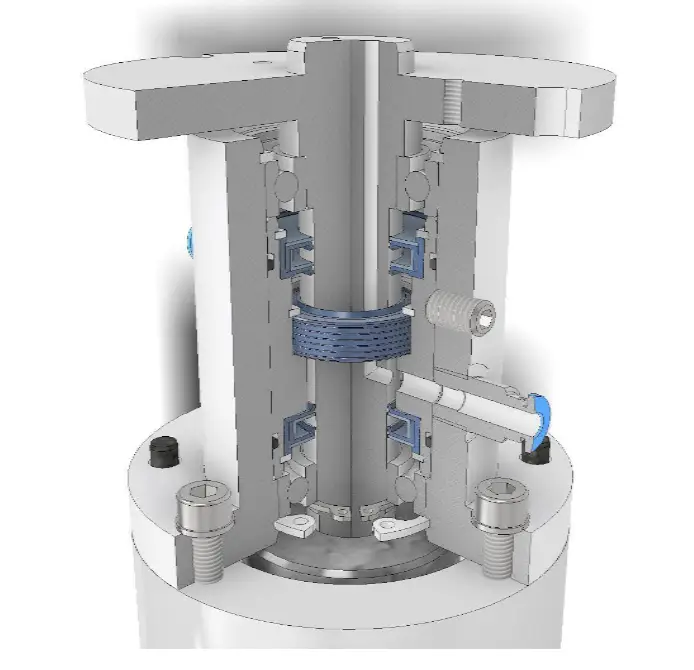
Design of the shaft
For reliable function and a long service life
service life of the sealing system, the precise
design of the shaft in the running surface area
is crucial. The following specifications for
design of the shaft must therefore be
to ensure that the dynamic sealing mechanism
in the contact area between the sealing lip and the
shaft is not unbalanced.
Diameter tolerance: ISO h11
Roundness tolerance: IT 8
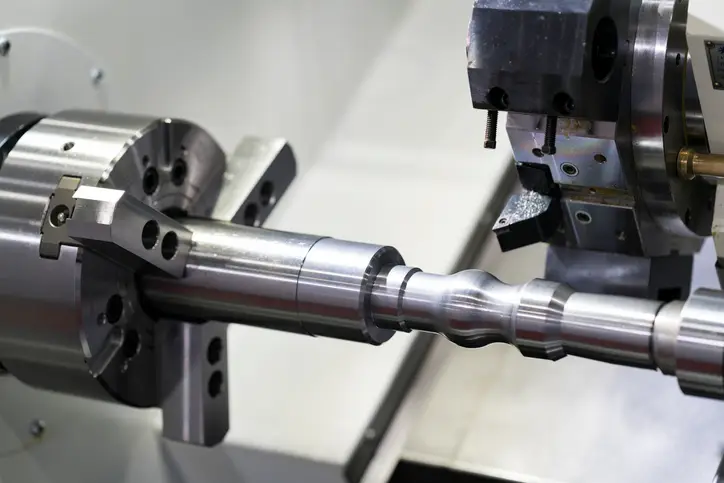
In many cases, standard stainless steel can be used without hardening.
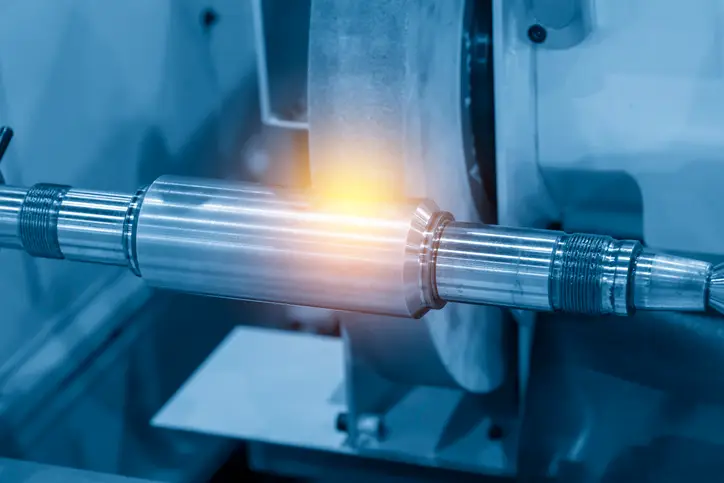
Surface quality
Ra = 0,2 – 0,8 μm
Rz = 1 – 5 μm
Rmax ≤ 6,3 μm
Hardness
The surface hardness of the shaft also has a
also has a major influence on the service life of the entire
sealing system.
25 – 30 HRC for simple applications
min. 40 HRC for normal applications
min. 55 HRC for external dirt ingress or with contaminated media,
Machining Process
The machining process of the shaft surface in the area of the rotary shaft seal significantly influences the reliable function of the entire sealing system. Achieving the required surface quality depends on the choice and quality of the machining process.
Freedom from Twist
The mating surface of the shaft should be free of twist or orientation. During machining, a twist orientation (similar to a micro-thread) can develop, causing the medium to be conveyed. Depending on the direction of rotation, this can either support or counteract the sealing effect of the radial shaft seal. If the twist orientation of the shaft exceeds that of the shaft seal, leakage will occur. In applications with only one direction of rotation, this behavior can be used to enhance the sealing effect.
Plunge Grinding
To create a torsion-free surface, we recommend plunge grinding (without axial feed). However, specific parameters must be observed to ensure a twist-free surface:
– The speed ratio between the grinding wheel and the workpiece must not be a whole number.
– Orientation can transfer to the grinding wheel. Therefore, use multi-grain dressing tools with the lowest possible axial feed or professional dressing rolls.
– The dressing time should be as long as possible until complete burnout is achieved.
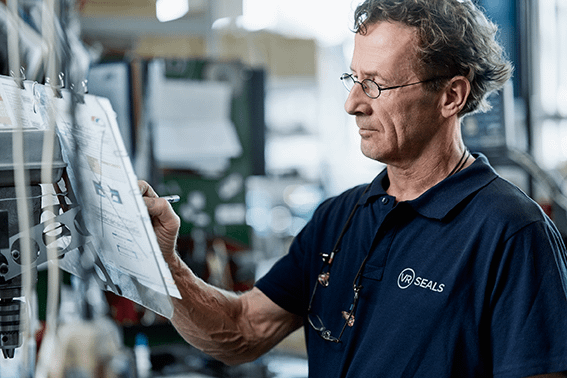
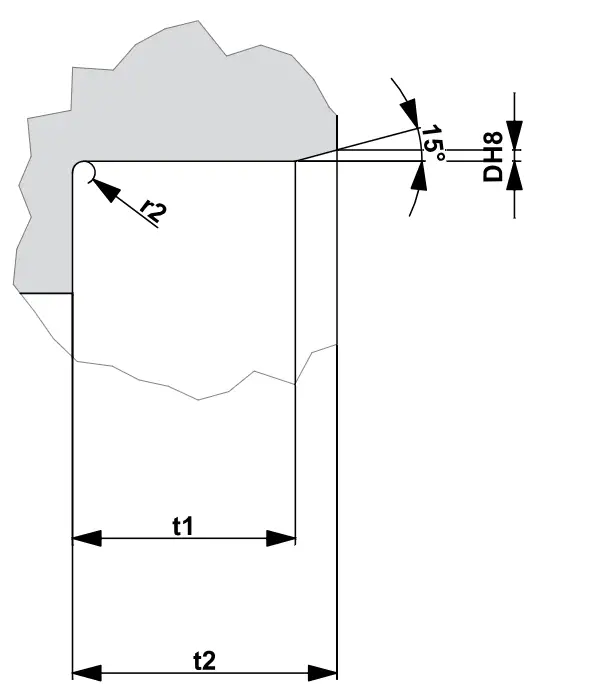
Housing bore
In addition to the dynamic seal between the seal lip and the shaft, a radial shaft seal also provides a static seal between its outer diameter and the locating bore. The precise design of the locating bore is crucial to prevent leakage between the seal’s outer face and the housing, ensuring a secure and tight fit.
t1 = B * 0.85 (minimum)
t2 = B + 0.3 mm (minimum)
r2 = 0.7 mm (maximum)
Concentricity and coaxiality according to DIN 3760